Vacuum Infusion Manufacturing Robot End Effector
The manufacturing method for large carbon fibre reinforced plastic (CFRP) aerospace components has long been a highly manual labour process and therefore is very costly.
Our goal was to develop a proof of concept robot end effector for semi-automating the highly labourous vacuum bagging pleating process, one of the major tasks involved in the vacuum assisted resin transfer molding AKA vacuum infusion process for fibre-reinforced plastic manufacturing (FRP).
The project involved a holistic and iterative design process to tackle cooperative human-robot manipulation tasks found in the unstructured manufacturing environment.
Please see the video demo showcasing our end-effector being controlled together with the Barrett Wam arm by CARIS UBC researchers.
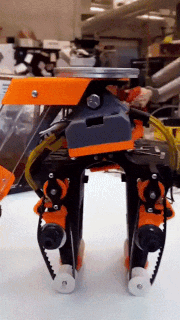
Key design features:
- Mechatronics:
• dexterous 2-DOF end-effector with compliant-actuated grip
• custom designed PCB w/ 58 components & WIFI module
• 8 sensors for detecting proximity, force contact, current, and tilt
• lightweight (1.1kg)
• 2 ways to manipulate target:• controlled pleat manipulation via belt driven high friction rollers
• smoothing action applicator via low friction pad - Firmware:
• real-time DC motor voltage and current control (for speed and torque control)
• real-time sampling, processing, and streaming sensor data
• WIFI communication with ROS protocol for integration w/ robot arm and logging data from sensors
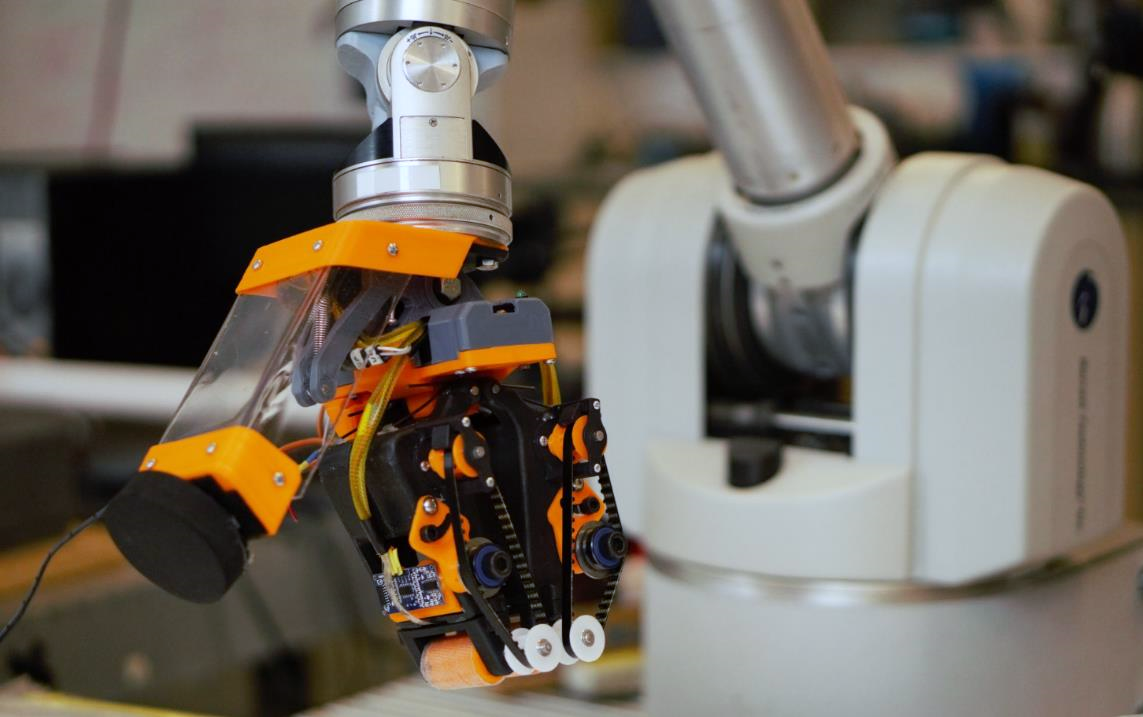
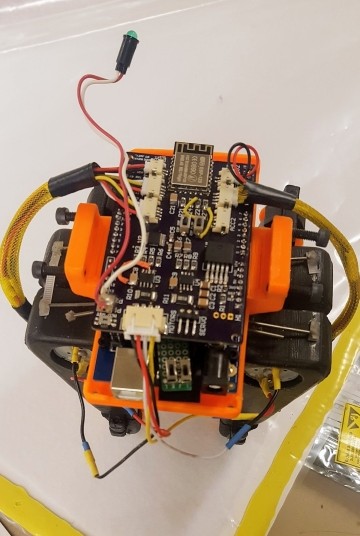
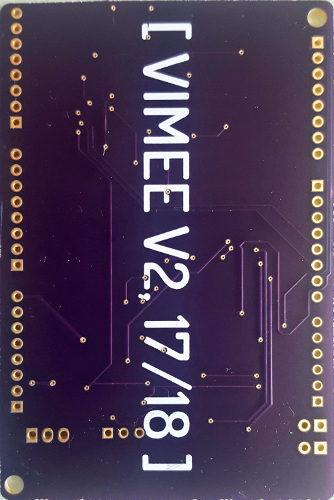
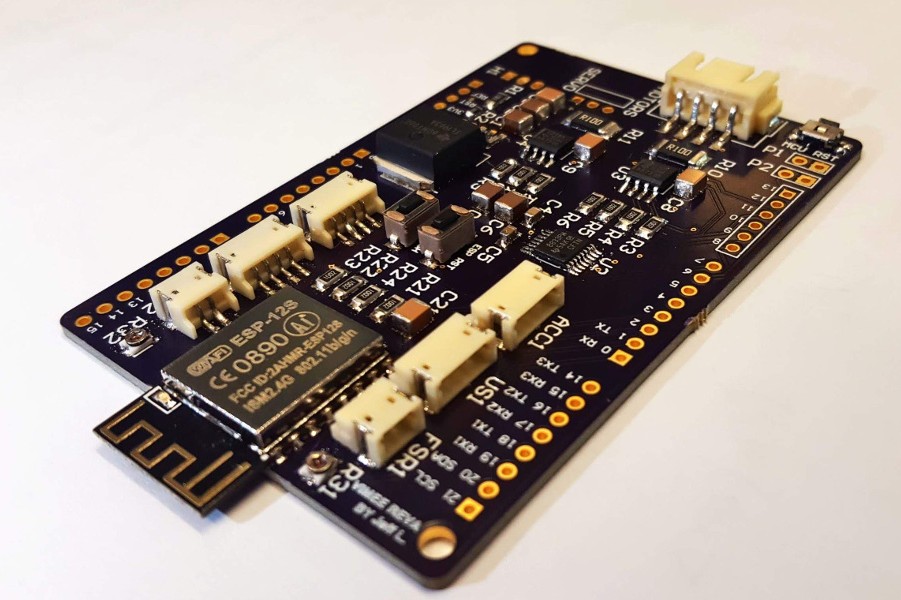

Combined with CARIS's robot arm and their augmented control system with HoloLens (AR headset) and Myo (myography armband) , the operator can control the end-effector's action, position, and pose. The end-effector can detect the environment with its force and proximity sensors, wirelessly transmitting the data to the controller to assist the vacuum bag manipulation process.